pp加工のしくじり先生が教える
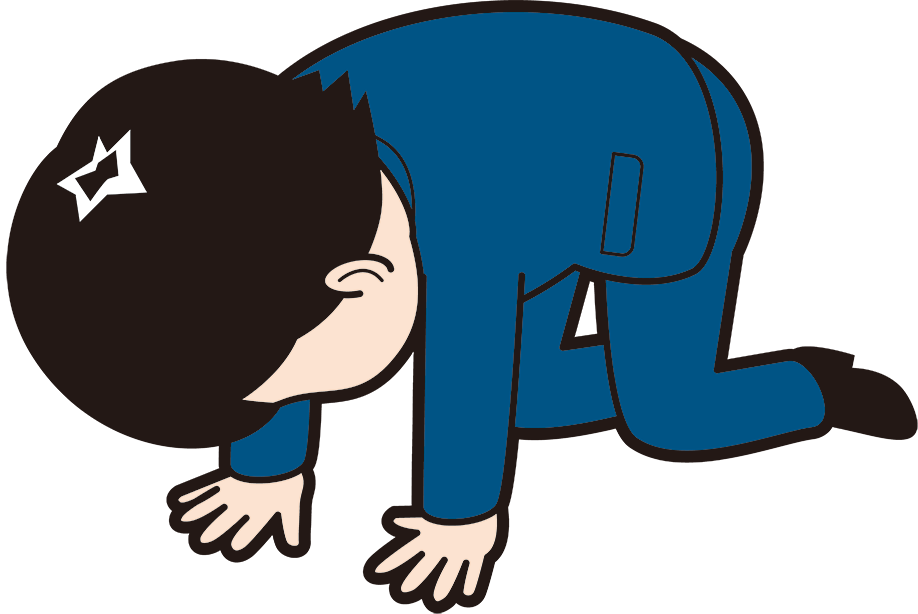
失敗から学んでください
pp加工のしくじり先生が教える失敗大全集
印刷の仕事の中でも、特にpp加工などの表面加工はそんなに頻繁に注文があるわけでないので、印刷経験豊富の営業マンでも、いざ受注すると売上がたつ反面、少し不安になるのではないでしょうか?
表面加工に限らず印刷の仕事は、トラブルという目に見えない『落とし穴』の連続です。印刷の仕事は目に見えない『落とし穴』を上手く避けながらいかに『納品』という目的地最短でたどり着くかということにつきます。
私の経験を話すと、この30年間『落とし穴』に落ちた経験は1度や2度じゃありません。落とし穴にはまり、落とし穴から出たら、また落とし穴にはまる。そんなことの繰り返しでした。だけど常に『次にその落とし穴に落ちないためにはどうすればいいか』と考え続け、この仕事を30年続けてきました。
おかげ様で最近ではそれほど落とし穴にはまることもなく、お客様に的確なアドバイスができるようになりました。ある意味そのような失敗やトラブルが私の経験を豊富にして育て上げてくれたといっていいかもしれません。
しかし失敗しないでスマートに仕事した方がいいにきまっています。印刷の大きな仕事は致命傷になりかねません。そこで経験30年の中で失敗してきたことを、皆様に公表し是非皆様のお仕事のお役に立てればと思います。特に印刷会社や広告代理店の方は、他人の失敗を自分の経験だと思い、仕事に活かしてください。
pp加工.com 藤井 眞治
目次(気になるタイトルをクリックしてください)
【PP加工編】
- グロスPP加工を施して納品をしたら色調でクレームになり全数刷直しを命じられた。
- 箔押し用のPPを貼ったら裏面にブロッキングのような現象が生じた。
- 印刷の色調基準が大変厳しいスポーツ用品のパッケージ(箱)色校正を取りマットPPの見本貼りを提出したのにも関わらず、マットPP加工を施し製品になった印刷物に対して色調でクレームになり全数刷直しを命じられた。
- PP加工後、すぐに断裁をしたらトンボの先端からPPが剥がれてしまった。
- 企画サイズ外の印刷物であった為、咥え尻、針、針尻に余白が全くない刷本がとどけられた。
- 裏面で印刷汚れがありクレームになり全数刷直しになった。
- 片面PP加工を施して納品したら反りはクレームになると言われた。
- マットPPを表紙面に貼ったらキズが付いていてクレームになった。
- 手提げ袋専用のPP貼り価格を間違えて通常のPP貼りの価格で見積書を提出し受注してしまった。
- 通常のグロスPP(艶あり)加工なのにマットPPを貼ってしまった。
- 線綴じのカタログにおいて表紙の裏面(表2・表3)の背の部分にベタの印刷がある為、製本屋さんでくるめない(糊が付かない)と言われた。
- 印刷費用を抑える為、輪転機(高速印刷機)でカタログの表紙を印刷した刷本に対してPP加工のご依頼がありました。
- 費用を抑える為に菊全機で付け合わせ印刷をして、後で断裁してA4部分だけを表面加工会社に刷本を渡したらPPを貼れないと断わられた
- 73Kg(四六ベース)の用紙にPP加工を依頼したら表面加工会社から貼れないと断られた。
- オンデマンド印刷でオンデマンド専用のフイルムを貼ったのに剥がれてしまった。
【プレスコート編】
- 表面加工会社にプレスコートを依頼し、用紙を上質紙で印刷したことを告げたら加工は出来ませんと断られた。
- 薄い用紙(4/6ベース135Kg)で菊全に多面付けした刷本に対してプレスコートの依頼をしたら表面加工会社から出来ないと断られた。
- 両面プレスコートを依頼したら両面には艶が出ないと言われた。
- 当日印刷した刷本にプレスコート加工をしたら艶があまり出ていなかった。
- 薄い用紙(4/6ベース 110Kg)4/6 4切判で印刷し、プレスコート加工を依頼したら表面加工会社から断られた。
【ビニール引き編】
【UVシルク印刷編
- グロスPP加工を施して納品をしたら色調でクレームになり全数刷直しを命じられた。
- 注意
グロスPPは艶感がハッキリと再現されます。特に赤のインキが強調された用に感じられます。食品、洋服、車、会社のロゴ等、品質が厳しい印刷物も相当あります。せっかく色校正を何度もやり直して色校正を提出したのにPPを貼ったらクレームになったのでは大変残念です。色校正が出来上がりましたらサンプルPPを貼ってお客様に確認していただき御了解を得てください。その際、表面加工会社に見本用と本番用のフイルムは同じ物を使用してくださいと伝えてください。(メーカーの相違があると若干見え方が違うかも知れません。)
- 箔押し用のPPを貼ったら裏面にブロッキングのような現象が生じた。
- 注意
加工ご依頼のお客様で後工程において、本来、箔押しは無いのに「箔押し」有に○が付けられた発注依頼書が届いた為、現場の作業者は迷わず「箔押し」に対応するフイルムを貼り作業を進めた。その結果、裏面にブロッキング(インキ跡)のような現象が発生し消込作業に追われ納期に間に合わなかった。 お互いの確認不足ですが、発注書はしっかり記入し再確認をして ご依頼をお願い致します。箔押し用のPPはコロナ処理(印刷特性、コーティング特性、密着特性が向上する電解処理)をされたフイルムで感度が大変高い為、ベタが多い印刷物には過剰に反応してフイルム上面までインキを運んでしまい刷本にインキが付着してしまう場合があります。今回のご対応方法は刷本のインキをウエス(シンナーの用な物)で拭き取る作業があった為、相当な時間が掛かり次工程に遅れが生じてしまいました。
- 印刷の色調基準が大変厳しいスポーツ用品のパッケージ(箱)色校正を取りマットPPの見本貼りを提出したのにも関わらず、マットPP加工を施し製品になった印刷物に対して色調でクレームになり全数刷直しを命じられた。
- 注意
PP加工の見本貼りの作製方法は2種類あります。
① 刷本が実際に機械で動いている状態で印刷物の上に別の印刷物を乗せPPを貼り、後に回りをカッターで剥がす。
② 本番と同じ様に給紙機にセットして機械を動かして見本を作成する。
今回の事故は①で行い見本の印刷物も実物より小さく用紙の斤量も異なり、用紙自体も凹凸がある紙であった為、フイルムの密着性の関係で色調が異なって見えた為、クレームになったのではないかと思います。①の方法では印刷物の上から印刷物を重ねますのでフイルムの密着度が高まります。見え方もハッキリしたイメージになります。色調基準の高い印刷物には見本といえども細心の注意が必要です。今回のご対応方法は印刷物を刷直していただいて、一度マットPPを貼り、再度刷本を給紙機に戻し空通し(フイルムをセットしない状態)で熱を上げ回転速度も低速にして密着力を高め、PP貼りを致しました。ほぼ見本と同じ様な見え方になりました。
- PP加工後、すぐに断裁をしたらトンボの先端からPPが剥がれてしまった。
- 注意
PP貼りは基本的には直ちに密着しますが、ベタが多い印刷物などには硬化するまで4〜5時間掛かる場合もありますので出来るだけ当日の作業は行わない方が良いと思われます。
- 企画サイズ外の印刷物であった為、咥え尻、針、針尻に余白が全くない刷本がとどけられた。
- 注意
本来PP加工を施す場合は天地左右10mm程の余白がないと安定的に作業が行えません。PP貼りは咥え尻に重なった状態で貼られて行きますので重ねのピッチの設定をギリギリで行いますと、ヤレも大量に発生し実数も割れる場合もあります。またピッチをクリアーしても内トンボにフイルムの重ね跡(接着剤の跡で白い線に見える)が発生します。ベタが多い印刷物ではかなり目立ちます。針、針尻に関しても内トンボ内にPPが貼られていないものや、刷本からフイルムがはみ出た状態になりますので、次工程でトラブルになります。印刷の面付けの設計には十分に注意が必要です。今回のご対応、方法はお客様にご理解をいただいてギリギリのピッチ設定で、刷本もベタがなかった為、重ね跡もほとんど目立たず回転速度も落として加工をした結果、特に大きな問題なく加工が出来ました。
- 裏面で印刷汚れがありクレームになり全数刷直しになった。
- 注意
PP加工をする上で本来オペレーターは両面とも目視チェックを行っていますが、全数はチェック出来ません。何故ならば印刷機と同じ様にPPの機械も回転速度が速い為、チェックが出来ないのです。ベタが多い印刷物は十分に乾燥時間を取り、サンプリングチェック(50枚〜100枚で1部を抜いて刷本をチェックする作業)も細かく設定されると良いと思われます。今回のご対応方法は二回目に再度同じ事故起きないようにUV機で印刷した刷本をいただきPP加工を施した結果、全く問題なく加工ができました。
- 片面PP加工を施して納品したら反りはクレームになると言われた。
本来、薄い用紙に片面PP加工を施す場合は必ず反りは発生します。片面に100度の熱とフイルム、接着剤が密着しますので片面に負荷が掛かるのは防ぎようがありません。季節や用紙、印刷物のベタ使用量も大きく関係しますが反りを出来るだけ抑えるのであればベタはあまり使用しないデザインが良いと思われます。今回のご対応方法はそれでも「お客様が納得していただけない」とのことで、裏面にもPPを貼る事をご提案致しました。結果的に両面PP加工を施した事によりほぼ反りは無くなりました。
- マットPPを表紙面に貼ったらキズが付いていてクレームになった。
- 注意
マットPP貼りはキズが付きやすく後工程での製本機での羽の接触や刷本の乱暴な扱い等などで簡単にキズが付きます。(爪で軽く擦っただけでキズが付きます)対処方法としてはベルベットPPというキズが付きにくいマットPPがありますが若干、割高になります。コスト面からあまり需要がない為、表面加工会社で扱っているところは少ないと思われます。今回のご対応としてはマットPPの欠点をご説明し、ベルベットPPの価格帯もご提示の上、ご検討されるとの事でした。
- 手提げ袋専用のPP貼り価格を間違えて通常のPP貼りの価格で見積書を提出し受注してしまった。
- 注意
手提げ袋を製作する場合には裏面の、のりしろに必ず糊付けをする必要があります。手提げ袋の、糊付けの方法は2種類あります。
① のりしろに手作業で強粘着の両面テープを貼る。
② サック貼りの機械で自動的に糊付けをする。上記①の場合、小部数であれば内職作業で対応出来ますが大量ロットの場合には内職作業代及び納期の関係で適していないと思われます。よって②のサック貼り専用のPPを貼ります。その際、通常のPP貼りをしてしまうと糊付けが全く出来ません。コロナ処理(印刷特性、コーティング特性、密着特性が向上する電解処理)されたフイルムを貼ります。今回のご対応としてはPP加工前だった為、のりしろ部分を逃がした状態で通常のPP貼作業を行いました。(咥え、針側は数センチ程度であればPPを貼られない状態を作れます。)予算が合わない、利益を確保する場合等、多少作業時間が掛かりますが有効な方法と思われます。
- 通常のグロスPP(艶あり)加工なのにマットPPを貼ってしまった。
- 注意
マットPPはフイルムをコロナ処理(印刷特性、コーティング特性、密着特性が向上す電解処理)されたフイルムで上下面、密着性が良いフイルムです。よってマットPPの上面からでもグロスPPは貼れます。(逆の場合は不可です。)
- 無線綴じのカタログにおいて表紙の裏面(表2・表3)の背の部分にベタの印刷がある為、製本屋さんでくるめない(糊が付かない)と言われた。
- 注意
本来、無線綴じ本は本文を重ねていき糊付けをして、最後に本文と表紙を糊でくるみ固めていきます。その際、背の部分にオフセットインキが印刷されていると糊は付きません。印刷設計の際に背の部分には印刷しないように部分的に抜く設計をしなければなりません。今回のご対応方法として表面は通常の片面グロスPP(艶あり)加工のご依頼があった為、裏面にはサック貼り専用のコロナ処理(印刷特性、コーティング特性、密着特性が向上する電解処理)されたフイルムをご提案致しました。結果、糊も付き製本も問題なく出来ました。
- 印刷費用を抑える為、輪転機(高速印刷機)でカタログの表紙を印刷した刷本に対してPP加工のご依頼がありました。
- 注意
輪転機で印刷した用紙はPP加工する上では適してはいません。何故ならば輪転機は紙にテンション(用紙を引っ張る)を掛け、水を使い、高熱で乾燥しカットされて排出されます。よって紙の寸法にバラつきが出ます。(最大で3mm程度の紙サイズのバラつきがあります。)その状態では給紙器にセット出来ません。PP加工をする際にはピッチ(紙の送り)の設定をした上で機械が動きますので内トンボにPPが貼られているものや、貼られてないものが出てきますので、必ずクレームになります。今回のご対応方法としては、用紙を揃えていただき、紙のサイズを同じ様に断裁して頂き、上記内容のご説明をご理解された上で作業を進めました。
- 印刷費用を抑える為に菊全機で付け合わせ印刷をして、後で断裁してA4部分だけを表面加工会社に刷本を渡したらPPを貼れないと断わられた。
- 注意
表面加工会社にもよりますが小さなサイズは加工が出来ない所はあります。どんなに小さなサイズでも用紙寸法300×400位のサイズがないと機械に掛かりません。それでも付け合わせ印刷をしなければいけない状況であるならば四六全の用紙を使用し、A4部分の回りを300×400の余白を付けられる様に設計すればPP加工は出来ます。
- 73Kg(四六ベース)の用紙にPP加工を依頼したら表面加工会社から貼れないと断られた。
- 注意
PP貼りの機械は本来、厚紙の方が作業効率的に良いのです。回転数も上がり、ヤレ(失敗分)もあまり出ません。73Kgの薄い用紙は給紙器からフイルムを貼るユニットにカール(片面に反り)がある為、安定的に用紙が送られません。また、たまたま送られても片面に100度の熱とフイルム、接着剤が密着しますのでより一層カールが激しくなります。またフイルムのしわも発生し、フイルムをカットするユニットに行き着く前に用紙が詰ります。よってヤレも大量に発生し場合によっては印刷予備が少ない場合、実数を割るケースもあります。表面加工会社も作業時間も掛かり、ヤレでフイルムのロスがかなり発生する為、あえて受注しないのではないかと思われます。弊社でも実績はあります。PP加工をする上で機械のそれぞれの特性を十分に理解しているオペレーターが作業をすると、(刷本の状態にもよります。)案外、作業が出来てしまう場合もありますので是非一度、ご相談をお願い致します。
- オンデマンド印刷でオンデマンド専用のフイルムを貼ったのに剥がれてしまった。
- 注意
オフセットインキとオンデマンドのトナーではPP加工をする上では大きな問題があります。通常オフセットインキで印刷された刷本に対しては、どんな用紙でも、ほぼ問題なく貼れるのに対してオンデマンド印刷された刷本はPPを貼っても簡単に剥離してしまう現象が発生します。その問題を解決すべく登場したのが「オンデマンド専用フイルム」です。このフイルムを貼れば全てのオンデマンド印刷に対応出来るのかと言われれば、そうではありません。オンデマンド印刷の場合は用紙の種類やトナーの量などの関係で加工をしても剥がれるケースもあります。また同じ用紙を使用してもプリンターのメーカー等の違い、トナーのメーカー等の違いで剥離する場合もあります。この剥がれの問題はフイルムメーカーでも現状は解決されていません。よってこの問題を解決する為には、エマルジョン加工を用いてPP貼りを行います。エマルジョンとは水溶液を用いてフイルムに接着剤を貼り(通常のPP加工においては接着剤が付いているフイルムを使用します。)低温で加工します。(通常のPP加工では100度〜110度の熱で低温の場合は50度程の温度で熱密着させます。)この方法で加工をすればまず問題はないのですがそれでも密着が弱い場合は回転速度を落とし、密着力を高め、温度設定も微妙に変化させて加工をします。このようなことからまだまだオンデマンド印刷には問題が残されています。オペレーターの経験値や手腕に頼るケースも多々あります。
グロスpp
オンデマンド印刷でオンデマンド専用のPPをはりましたがトンボ部分から若干の抵抗もありましたが、強く引っ張ったら剥がれてしまいました。マットpp
オンデマンド印刷でオンデマンド専用のPPをはりましたがトンボ部分から若干の抵抗もありましたが、強く引っ張ったら剥がれてしまいました。
【プレスコート編】
- 表面加工会社にプレスコートを依頼し、用紙を上質紙で印刷したことを告げたら加工は出来ませんと断られた。
- 注意
プレスコートの加工は用紙に艶を出す塗布加工(コート紙)をしてあるものではないと加工は出来ません。プレスコート加工をしても全く艶が出ません。プレスコートは用紙の塗布を利用し溶剤を塗り、乾燥させ、熱圧着で艶を出します。今回のご対応方法としてはPP加工のようにフイルムを貼ることは環境問題が問われると言うことで、LCコートをご提案致しました。LCコートはフイルム貼りではなく、熱転写でPPを貼った様な艶が出ます。プレスコート程ではないと思われますが、ほぼ問題はないと思われます。
- 薄い用紙(4/6ベース135Kg)で菊全に多面付けした刷本に対してプレスコートの依頼をしたら表面加工会社から出来ないと断られた。
- 注意
プレスコート加工を施す際、給紙器から搬送路を通り溶剤のユニットに搬送されます。
(搬送路と溶剤ユニットは直結しています。)その際、薄い用紙ですと機械の構造上用紙が暴れて安定的に溶剤のユニットに用紙を搬送出来ません。対策として搬送路に上面より糸を取り付けて(1本〜3本)刷本の余白部分に糸を張り、暴れを防ぎます。糸を取り付けることで暴れの問題は解決出来ますが、問題は多面付けをしていると余白がほとんど無いため、トンボ内に糸の剥がし跡が付きます。溶剤が乳白色の為、濃いベタですと白い線がハッキリと目立ちます。それを回避する為にも余白は必ず必要とします。用紙の斤量、面付け、印刷物の内容にもよりますが場合によっては大きく余白が必要になるケースもありますので、印刷設計の際、多面付けには注意が必要です。今回のご提案方法としては、印刷物の品質は重要とのことでしたので、この状態で(菊全の状態)でプレスコート加工を施し(面損する)、糸の剥がし跡が付いてしまった刷本は処分し、菊半で刷り増し、余白を大きく取り刷本に再度プレスコート加工をお勧め致しました。
- 両面プレスコートを依頼したら両面には艶が出ないと言われた。
- 注意
プレスコート加工の場合PP貼りのように両面に艶が出ません。プレスコートの艶を出すには下記のユニットを経て初めて光沢感が出ます。
* プレスコート加工をする場合は必ずコート紙を使用します。(塗布加工していないものは艶が出ません。)
① 刷本に溶剤を浸透させる。
② 刷本を熱風で乾燥させる。
③ 刷本を熱版で圧着させる。
以上のように①②③の工程を経て艶を出します。両面の場合、再度給紙器に刷本をセットし繰り返し作業をします。この際、一度艶を出した刷本が②③番を通過すると、艶が死んでしまった状態になります。(曇った印象に見えます)片面加工した印象とは断然に違いがありますので、両面プレスコートはお客様の了解を得てから作業を進行しないと必ずクレームになります。十分な注意が必要です。今回のご対応方法としては、両面LCコート(熱転写で艶を出す方法)をご提案致しました。LCコートであれば両面にPPのような艶も維持出来る為、問題はないと思われます。
- 当日印刷した刷本にプレスコート加工をしたら艶があまり出ていなかった。
- 注意
全ての加工に言えることですが刷本が完全に乾いていないと様々な事故を引き起す可能性があります。刷本どうしのブロッキング、プレスコート機のユニットにインキ跡が付着する事故等、様々な問題を発生させます。UV印刷のように水を全く使用しない印刷機であれば問題はないのですが,オフセット印刷の場合、水を使用して印刷します。目に見えない水分が用紙の表面にあります。今回の現象はオフセットインキの乾燥不足、水分を含んでいる刷本に問題があります。水分を含んでいると熱版で圧着しても思い通りの艶が期待出来ません。特にベタが多い場合、表面上は乾いている様に見えても用紙内部でインキ、水が乾いていない場合がありますので十分に乾燥時間が必要とされます。
- 薄い用紙(4/6ベース 110Kg)4/6 4切判で印刷し、プレスコート加工を依頼したら表面加工会社から断られた。
- 注意
ご相談内容としては4/6 4切判で両サイドに余白があり、印刷の絵柄もベタが少ないのに何故加工が出来ないのかと言う事でした。判サイズ、余白があることは条件をクリアーしていますが、問題は用紙の薄さです。プレスコート加工は溶剤の層を通りドライヤーのユニットを経て熱版(ステンレス版)にて圧着して艶を出します。その後、熱版から刷本を剥離して排出口に落とします。ここで問題となるのが用紙の薄さです。熱版は密着力が高く、薄い用紙ですと剥離せず、版に巻き付いたまま次の用紙を受け入れてしまい紙と紙がぶつかり熱版のユニットで用紙が詰ります。場合によっては版にキズが付きます。コンピュータ制御でエラーになり機械が停止すれば問題はないのですが機械の構造上そのような機能が無いため、人力の作業になります。作業効率も悪く、熱版へのキズ、ヤレもかなり出る為、あえて受注しないのではないかと思われます。弊社でも実績はあります。機械の特性を十分に理解しているオペレーターが作業をすると、(刷本の状態にもよります。)案外、作業が出来てしまう場合もありますので是非一度、ご相談をお願い致します。
【ビニール引き編】
- ケーキの箱を納品したら水分が浸透して箱がヨレヨレになりクレームになった。
水分を含んでいる食品を直においたらボール紙といえども水分を吸収してしまいます。さまざま箱の受注をしているとついつい忘れがち(ほとんどの箱はビニール引きがありません。)ですが、直置きの食品箱は必ず耐水性を持たせる為、ビニール引きが必要になります。「ビニール引きって何」というご相談を受けますがビニール引きはスーパーにある様なビニール(肉や魚の汁を出さない為の袋)とは違います。印刷で例えて言えばOPニスのような見た目で溶剤を刷本に塗布します。OPニスの役割はインキ止め(濃いベタが絵柄にある場合ニスを塗布することでブロッキングを防ぎます)や印刷物の見た目(艶がある様に見える)の役割をしますが、ビニール引きはブロッキングの効果もありますが役割としては大きな違いがあります。「塩化系合成ビニール樹脂」と言う塗料を使用します。ちょっと、いかつい感じはしますが人体、環境には全く問題はありません。そして水性塗料を使用しますので食品にも影響が無い溶剤です。
【UVシルク印刷編】
- オフセット印刷で多面付けした刷本(菊全32面付け)にUVシルク印刷を業者に依頼したら印刷の文字がずれていた。
- 注意
今回のご相談は何故、印刷がずれたのか、責任の所在はどこにあるのかとのことでした。ご相談内容からしてオフセット印刷の針飛びだと思われます。針飛びとは刷本が蛇行せず針にきちんと当たればマークの用な物を印刷します。このマークが刷本に付いていないと蛇行して印刷されたことになります。こんな事をいっては叱られるかも知れませんが、印刷に関わっている業者様は絶えず危険と隣合わせだと思います。なにぶん、機械が作業をしていることなので全てをチェックすることが出来ないからです。それではまずオフセット印刷の分析をしてみたいと思います。用紙を給紙器にセットして正常に紙が送られるかチェックします。問題がなければ印刷をスタートします。スタート直後は4Cインキが安定せずガラ出し作業(インキが安定的に維持出来るまでの作業)を行います。その際、刷本が針にしっかり当たっているかもチェックします。印刷が安定して来たらサンプリングチェック(100枚〜200枚印刷したら1部抜き、刷本をチェックする作業)を行います。オペレーターはこの作業を繰り返します。これほどしっかりチェックしているのにも関わらず事故は起こります。サンプリングチェックでは問題が無いのに、いざ本番の刷本を納めUVシルク印刷をしたら文字がずれて印刷されていたと言うことは時々聞きます。UVシルク印刷も完璧ではありませんがオフセット印刷に比べ回転速度は遅い為、事故の可能性は低いと思われます。いずれにしても後工程においての品質が重要になります、お互いの業者が印刷後のチェック態勢をしっかり確認しないと重大な問題になる可能性があります。